Difference between revisions of "Key Design and Plan Review Considerations"
Dean Young (talk | contribs) |
Dean Young (talk | contribs) |
||
(14 intermediate revisions by the same user not shown) | |||
Line 4: | Line 4: | ||
==Overview== | ==Overview== | ||
− | Designing LID practices and treatment trains with ease and cost of inspection and maintenance in mind is critical to the affordability of municipal stormwater infrastructure asset management programs and must be considered early on in planning and design processes. The following sections provide strategies to help limit the frequency of rehabilitation or repair work, make routine inspection and maintenance tasks easier to perform, and ensure they are | + | Designing LID practices and treatment trains with ease and cost of inspection and maintenance in mind is critical to the affordability of municipal stormwater infrastructure asset management programs and must be considered early on in stormwater management system planning and design processes. The following sections provide strategies to help limit the frequency of rehabilitation or repair work, make routine inspection and maintenance tasks easier to perform, and ensure they are functioning adequately over their operating life cycle. |
==Provide Runoff Pretreatment== | ==Provide Runoff Pretreatment== | ||
− | To treat runoff from highly trafficked pavements with LID practices it is wise to include [[Pretreatment| pretreatment]] features or components that capture and isolate sediment from the rest of the facility in the design. [[Pretreatment]] refers to techniques or devices used to retain coarse materials suspended in stormwater runoff, either through filtration or settling, before it enters the BMP rendering it inefficient over time. Proper pretreatment extends the operating phase of the BMP’s life cycle by reducing the rate of accumulation of coarse sediment, thus delaying the need for at times expensive structural repairs like unclogging filter beds, pipes and orifices. Common pretreatment devices include [[vegetated filter strips]], [[Enhanced swales|grass swales]], [[geotextile]]-lined inlet filters/liners, [[check dams]], [[forebays]], eavestrough screens or filters, [[Oil and grit separators| oil and grit separators]] (i.e., hydrodynamic separators) and catch basins or manholes containing baffles, filters and sumps. One important consideration for pretreatment is that these devices require frequent (e.g., annual) sediment and trash removal maintenance and should be easy to access by personnel, vehicles and equipment needed to perform inspection and maintenance tasks. From an operation and maintenance perspective, a good strategy is to select or design pretreatment features or components that | + | To treat runoff from highly trafficked pavements with LID practices it is wise to include [[Pretreatment| pretreatment]] features or components that capture and isolate sediment from the rest of the facility in the design. [[Pretreatment]] refers to techniques or devices used to retain coarse materials suspended in stormwater runoff, either through filtration or settling, before it enters the BMP rendering it inefficient over time. Proper pretreatment extends the operating phase of the BMP’s life cycle by reducing the rate of accumulation of coarse sediment, thus delaying the need for at times expensive structural repairs like unclogging filter beds, pipes and orifices. Common pretreatment devices include [[vegetated filter strips]], [[Enhanced swales|grass swales]], [[geotextile]]-lined inlet filters/liners, [[check dams]], [[forebays]], eavestrough screens or filters, [[Oil and grit separators| oil and grit separators]] (i.e., hydrodynamic separators) and catch basins or manholes containing baffles, filters and sumps. One important consideration for pretreatment is that these devices require frequent (e.g., annual) sediment and trash removal maintenance and should be easy to access by personnel, vehicles and equipment needed to perform inspection and maintenance tasks. |
+ | |||
+ | From an operation and maintenance perspective, a good strategy is to select or design pretreatment features or components that either the municipality or property owner will already have the capacity to maintain. While ease of inspection and maintenance is an important consideration, maintenance costs may not always be lowest for the easiest options if they require special or expensive equipment. For example, easily accessible pretreatment features like filter strips or forebays that can be maintained manually with typical landscaping equipment will be cheaper to maintain than underground sumps that need to be jet washed and vacuumed using a hydro-vac truck. | ||
[[File:Oil-grit separator USGS 2002.png|thumb|350px|Example oil-grit separator USGS 2002 (Wikimedia commons)]] | [[File:Oil-grit separator USGS 2002.png|thumb|350px|Example oil-grit separator USGS 2002 (Wikimedia commons)]] | ||
Line 20: | Line 22: | ||
*When designing stormwater infiltration BMPs, consideration should be given to where the majority of trash, sediment and debris will accumulate in the BMP and where snow storage will occur (a significant source area for sediment and debris). | *When designing stormwater infiltration BMPs, consideration should be given to where the majority of trash, sediment and debris will accumulate in the BMP and where snow storage will occur (a significant source area for sediment and debris). | ||
*Infiltration BMPs should include [[pretreatment]] devices, inlet designs or forebays that allow accumulation to occur without blocking inflow (e.g., 5 cm change in grade between pavement surface and BMP surface) and that isolate sedimentation areas from the main portions of the filter bed so that the area disturbed through routine sediment removal maintenance is minimized. | *Infiltration BMPs should include [[pretreatment]] devices, inlet designs or forebays that allow accumulation to occur without blocking inflow (e.g., 5 cm change in grade between pavement surface and BMP surface) and that isolate sedimentation areas from the main portions of the filter bed so that the area disturbed through routine sediment removal maintenance is minimized. | ||
+ | *Designing LID practices and treatment trains as being part of the minor drainage system only is another strategy that helps control operation and maintenance costs. Designing conveyance systems such that during major storm events, once the storage capacity of the LID practice or treatment train of practices has been exceeded, flows are directed to the major drainage system avoids the need for protective features to safely convey high flows through the practice or treatment train, and their associated maintenance. | ||
==Inspection & Maintenance Features== | ==Inspection & Maintenance Features== | ||
− | + | All stormwater facilities and practices share a common design requirement for accessibility by personnel and equipment needed to perform inspection and maintenance tasks.<ref>Blecken, G.T., Hunt, W.F., Al-Rubaei, A.M. Viklander, M., Lord, W.G. 2017. Stormwater control measure (SCM) maintenance considerations to ensure designed functionality. Urban Water Journal. Vol.14, No.3, 278-290. https://www.tandfonline.com/doi/full/10.1080/1573062X.2015.1111913 </ref> Planning and design of LID practices and treatment trains should consider how they will be maintained (e.g., what equipment is needed?) and what features are needed to perform necessary inspection and maintenance tasks. For example, to understand whether or not an underground infiltration trench is draining at an adequate rate, features such as monitoring wells that extend to the bottom of the practice will be needed. Input on designs from staff who will be responsible for performing inspection and maintenance tasks should be sought to identify features that would make tasks easier to perform, and identify situations where the property owner does not have the necessary capacity or resources (e.g., special equipment, skill set or budget). | |
The following table provides some examples of inspection and maintenance features that should be considered in the BMP process: | The following table provides some examples of inspection and maintenance features that should be considered in the BMP process: | ||
Line 65: | Line 68: | ||
==Inclusion of Planting Plans== | ==Inclusion of Planting Plans== | ||
− | [[File:Kortright Planting Plan.PNG|700px|thumb|An example of a [https://wikidev.sustainabletechnologies.ca/images/a/ac/Bio-Retention_Cell-Cell_A_planting_plan_20130415.pdf | + | [[File:Kortright Planting Plan.PNG|700px|thumb|An example of a [https://wikidev.sustainabletechnologies.ca/images/a/ac/Bio-Retention_Cell-Cell_A_planting_plan_20130415.pdf planting plan] for a [[Bioretention]]/[[Bioswale]] located at the Kortright Centre, in Vaughan, ON. listed with appropriate [[plants]], [[grasses]], [[trees]] and [[shrubs]] species for the area with their scientific and common names listed along with the quantity to be planted, plant type, site and condition characteristics, flowering assemblages and colours and mature height (Source: TRCA, 2013.)|link=https://wikidev.sustainabletechnologies.ca/images/a/ac/Bio-Retention_Cell-Cell_A_planting_plan_20130415.pdf]] |
All vegetated BMP designs should include planting plans that specify [[Plant selection|species]] that can tolerate both wet and dry conditions and, for BMPs that will receive de-icing salt laden runoff during winter, species | All vegetated BMP designs should include planting plans that specify [[Plant selection|species]] that can tolerate both wet and dry conditions and, for BMPs that will receive de-icing salt laden runoff during winter, species | ||
− | that are salt tolerant. Further consideration should be given to species that are both pollution and soil compaction tolerant given the location of many BMPs along roadways and near public spaces. Where possible, planting should done during the wettest seasons/months of the year (e.g., early spring and mid-to-late fall) to help minimize the need for irrigation (and staff time and equipment) during the establishment/warranty period. Use of drought-tolerant and native species will help minimize or eliminate the need for irrigation during the operating phase of the BMP life cycle. Good vegetation cover on the surface and side slopes of BMPs helps to maintain infiltration function, contributes to runoff volume reduction function through evapotranspiration, and helps prevent erosion of soil and/or mulch cover from flowing overland water. | + | that are salt tolerant. Further consideration should be given to species that are both pollution and soil compaction tolerant given the location of many BMPs along roadways and near public spaces. Where possible, planting should done during the wettest seasons/months of the year (e.g., early spring and mid-to-late fall) to help minimize the need for irrigation (and staff time and equipment) during the establishment/warranty period. Use of deeply-rooting, drought-tolerant and native species will help minimize or eliminate the need for irrigation during the operating phase of the BMP life cycle. Planting with plugs, pots, caliper tree or shrub stock or sod is preferable over broadcast seeding approaches. Seeding requires stormwater practices to be kept off-line for a period of time following planting to allow germination and plant establishment to occur, and to be irrigated in the absence of adequate rainfall to ensure success. Good vegetation cover on the surface and side slopes of BMPs helps to maintain infiltration function, contributes to runoff volume reduction function through evapotranspiration, and helps prevent erosion of soil and/or mulch cover from flowing overland water. |
+ | |||
+ | Where a naturalized aesthetic is suitable, vegetated practices that feature native or perennial plants may be preferable as they require less maintenance than traditional, more manicured urban landscapes featuring turf grasses or annual-dominated decorative garden beds. <ref>DelGrosso, Z.L., Hodges, C.C., Dymond, R.L. 2019. Identifying Key Factors for Implementation and Maintenance of Green Stormwater Infrastructure. Journal of Sustainable Water in the Built Environment. 5(3): 05019002. https://ascelibrary.org/doi/10.1061/JSWBAY.0000878 </ref> A cost-efficient strategy for planting plan design is to focus on landscape types, aesthetics and plants that the municipality or property owner already has the resources to establish, inspect and maintain. | ||
Both common and botanical (i.e., species Latin name) names should be used on [[Planting design#Planting plans and specifications|planting plans]] so that inspectors and maintainers of the vegetation are better able to recognize or develop the means of recognizing the plants in the field and distinguishing them from pervasive weeds. Planting plans should also specify the planting method (e.g., seed vs. sod) and plant or container size (e.g., saplings vs. caliper tree; plugs vs. pots; bare root vs. root ball). Any deviations from the planting plan or species substitutions should be noted on as-built drawings/planting plans. | Both common and botanical (i.e., species Latin name) names should be used on [[Planting design#Planting plans and specifications|planting plans]] so that inspectors and maintainers of the vegetation are better able to recognize or develop the means of recognizing the plants in the field and distinguishing them from pervasive weeds. Planting plans should also specify the planting method (e.g., seed vs. sod) and plant or container size (e.g., saplings vs. caliper tree; plugs vs. pots; bare root vs. root ball). Any deviations from the planting plan or species substitutions should be noted on as-built drawings/planting plans. |
Latest revision as of 22:21, 23 November 2022

Overview[edit]
Designing LID practices and treatment trains with ease and cost of inspection and maintenance in mind is critical to the affordability of municipal stormwater infrastructure asset management programs and must be considered early on in stormwater management system planning and design processes. The following sections provide strategies to help limit the frequency of rehabilitation or repair work, make routine inspection and maintenance tasks easier to perform, and ensure they are functioning adequately over their operating life cycle.
Provide Runoff Pretreatment[edit]
To treat runoff from highly trafficked pavements with LID practices it is wise to include pretreatment features or components that capture and isolate sediment from the rest of the facility in the design. Pretreatment refers to techniques or devices used to retain coarse materials suspended in stormwater runoff, either through filtration or settling, before it enters the BMP rendering it inefficient over time. Proper pretreatment extends the operating phase of the BMP’s life cycle by reducing the rate of accumulation of coarse sediment, thus delaying the need for at times expensive structural repairs like unclogging filter beds, pipes and orifices. Common pretreatment devices include vegetated filter strips, grass swales, geotextile-lined inlet filters/liners, check dams, forebays, eavestrough screens or filters, oil and grit separators (i.e., hydrodynamic separators) and catch basins or manholes containing baffles, filters and sumps. One important consideration for pretreatment is that these devices require frequent (e.g., annual) sediment and trash removal maintenance and should be easy to access by personnel, vehicles and equipment needed to perform inspection and maintenance tasks.
From an operation and maintenance perspective, a good strategy is to select or design pretreatment features or components that either the municipality or property owner will already have the capacity to maintain. While ease of inspection and maintenance is an important consideration, maintenance costs may not always be lowest for the easiest options if they require special or expensive equipment. For example, easily accessible pretreatment features like filter strips or forebays that can be maintained manually with typical landscaping equipment will be cheaper to maintain than underground sumps that need to be jet washed and vacuumed using a hydro-vac truck.
Design Low Maintenance Conveyance Systems[edit]
The design of conveyance systems that carry stormwater into the BMP should anticipate potential maintenance issues and include features to minimize or avoid them.
For example, during large storm events, rapidly flowing water into or out of the BMP often causes erosion in vegetated practices. Inlet and outlet designs should consider protective features that prevent erosion. The size of inlets to BMPs and their slope also needs careful consideration as small, gently sloping openings are easily clogged with coarse debris and sediment which could cause stormwater flows to by-pass or not enter the BMP, increasing maintenance needs.
- Curb cuts should curve into the BMP so that flowing stormwater does not have to turn sharply to enter and inlets should be sloped at between 5 and 10%.
- Inlets should also be easily accessible and unobstructed by permanent covers to make trash, sediment and debris removal maintenance easy to perform.
- When designing stormwater infiltration BMPs, consideration should be given to where the majority of trash, sediment and debris will accumulate in the BMP and where snow storage will occur (a significant source area for sediment and debris).
- Infiltration BMPs should include pretreatment devices, inlet designs or forebays that allow accumulation to occur without blocking inflow (e.g., 5 cm change in grade between pavement surface and BMP surface) and that isolate sedimentation areas from the main portions of the filter bed so that the area disturbed through routine sediment removal maintenance is minimized.
- Designing LID practices and treatment trains as being part of the minor drainage system only is another strategy that helps control operation and maintenance costs. Designing conveyance systems such that during major storm events, once the storage capacity of the LID practice or treatment train of practices has been exceeded, flows are directed to the major drainage system avoids the need for protective features to safely convey high flows through the practice or treatment train, and their associated maintenance.
Inspection & Maintenance Features[edit]
All stormwater facilities and practices share a common design requirement for accessibility by personnel and equipment needed to perform inspection and maintenance tasks.[2] Planning and design of LID practices and treatment trains should consider how they will be maintained (e.g., what equipment is needed?) and what features are needed to perform necessary inspection and maintenance tasks. For example, to understand whether or not an underground infiltration trench is draining at an adequate rate, features such as monitoring wells that extend to the bottom of the practice will be needed. Input on designs from staff who will be responsible for performing inspection and maintenance tasks should be sought to identify features that would make tasks easier to perform, and identify situations where the property owner does not have the necessary capacity or resources (e.g., special equipment, skill set or budget).
The following table provides some examples of inspection and maintenance features that should be considered in the BMP process:
LID BMP Type |
Description |
---|---|
Infiltration BMPs | |
For infiltration BMPs, monitoring wells that extend to the bottom and standpipes or manholes connected to sub-drains that allow access for drainage performance verification through water level measurements and routine flushing of sediment from pipes. | |
For infiltration BMPs, sub-drain pipes should be 200 mm in diameter and be connected to manholes, maintenance hatches or standpipes (for standpipes, it is best to use two (2) 45 degree couplings) to allow for inspection by closed circuit camera (i.e., push camera) and sediment removal by jet-vac equipment. | |
Vegetated BMPs | |
For vegetated BMPs, consideration should be given to what source of water will be drawn upon for irrigation during the establishment/warranty period, how it will be delivered to the BMP (e.g., is equipment with sufficient volume and pressure available?), and in some cases an irrigation system should be part of the BMP design (e.g., green roofs). | |
For vegetated BMPs in high pedestrian traffic areas, consider the need for walkways or stepping stones and barriers to help limit foot traffic to designated portions of the BMP, or discourage it altogether if it is causing vegetation maintenance issues. | |
Underground Pretreatment or BMPs | |
For underground pretreatment devices or BMPs, the associated manholes or maintenance hatches should be close to a drivable surface/path that can support the heavy vehicles needed for sediment removal maintenance (e.g., hydrovac trucks) and consider installing a staff gauge or graduated measuring tape to allow sediment depth to be assessed visually from the ground surface, without having to enter the confined space. | |
Green Roofs and Blue Roofs | |
Safe and efficient means of accessing and exiting a green roof or blue roof site for installation, inspection and maintenance is a primary consideration as it will influence the time and effort required to transport tools, equipment and materials to and from the site. | |
For green roofs and blue roofs, tie-off points for ladders and personal fall protection safety equipment should be incorporated in the roof design for use by individuals performing inspection and maintenance work. | |
General Considerations | |
Lockable caps on monitoring wells and sub-drain clean-out standpipes to prevent unauthorized access, tampering, or vandalism. | |
Features for taking the BMP off-line or draining stored water by gravity to improve ease of inspection and sediment removal maintenance tasks. | |
Inlets should be readily accessible from surface conveyances, catchbasins, manholes or access hatches to avoid the need for specialized equipment for inspection (e.g., closed circuit or remote controlled cameras). |
Inclusion of Planting Plans[edit]
All vegetated BMP designs should include planting plans that specify species that can tolerate both wet and dry conditions and, for BMPs that will receive de-icing salt laden runoff during winter, species that are salt tolerant. Further consideration should be given to species that are both pollution and soil compaction tolerant given the location of many BMPs along roadways and near public spaces. Where possible, planting should done during the wettest seasons/months of the year (e.g., early spring and mid-to-late fall) to help minimize the need for irrigation (and staff time and equipment) during the establishment/warranty period. Use of deeply-rooting, drought-tolerant and native species will help minimize or eliminate the need for irrigation during the operating phase of the BMP life cycle. Planting with plugs, pots, caliper tree or shrub stock or sod is preferable over broadcast seeding approaches. Seeding requires stormwater practices to be kept off-line for a period of time following planting to allow germination and plant establishment to occur, and to be irrigated in the absence of adequate rainfall to ensure success. Good vegetation cover on the surface and side slopes of BMPs helps to maintain infiltration function, contributes to runoff volume reduction function through evapotranspiration, and helps prevent erosion of soil and/or mulch cover from flowing overland water.
Where a naturalized aesthetic is suitable, vegetated practices that feature native or perennial plants may be preferable as they require less maintenance than traditional, more manicured urban landscapes featuring turf grasses or annual-dominated decorative garden beds. [3] A cost-efficient strategy for planting plan design is to focus on landscape types, aesthetics and plants that the municipality or property owner already has the resources to establish, inspect and maintain.
Both common and botanical (i.e., species Latin name) names should be used on planting plans so that inspectors and maintainers of the vegetation are better able to recognize or develop the means of recognizing the plants in the field and distinguishing them from pervasive weeds. Planting plans should also specify the planting method (e.g., seed vs. sod) and plant or container size (e.g., saplings vs. caliper tree; plugs vs. pots; bare root vs. root ball). Any deviations from the planting plan or species substitutions should be noted on as-built drawings/planting plans.
All construction contracts that include vegetation should specify a minimum two (2) year warranty period (i.e., establishment period) for the plants, which begins after planting is completed, and ends when the BMP is assumed by the owner. Over the warranty/establishment period the contractor is responsible for routine maintenance tasks (e.g., watering, weeding, and sediment and trash removal).
Consideration should be given to specifying a phased approach to planting in construction contracts, in which planting occurs in two stages (e.g., fall and the following spring; spring and the following fall) to help ensure the full palette of plants specified in the plan are available. Thereby, any failed plantings from the first stage of planting are sure to be replaced in the second. If many or all plantings of a certain species do not survive the first phase, they can be substituted with another more tolerant or suitable species in the second (A list of suitable shrubs, trees, graminoids, etc. can be found on our Plant lists page).
Inclusion of Sediment Removal Plans[edit]
As mentioned previously, it is recommended that, where possible, pretreatment devices be included in BMP designs that help retain coarse sediment and debris in an easily accessible location before it enters the BMP itself. However even with pretreatment devices in place, fine sediment will inevitably reach the BMP and accumulate over time. LID BMP designs need to consider how sediment can be removed from associated manhole sumps, pretreatment devices, inlets and pipes, and include adequate features and routes for access by necessary equipment.
LID BMP Type |
Equipment Required for Sediment Removal |
---|---|
Permeable Pavers | For permeable pavements, regenerative air sweeper (for routine maintenance) or vacuum sweeper (for rehabilitation) equipment (e.g., street cleaner trucks or more compact units) will be needed, so designs should allow access to the majority of the surface by necessary equipment (e.g., minimize obstructions and sharp corners); |
Inlets, Grass filter strips, gravel diaphragms, Check dams, and Forebays | Use of a vacuum sweeper truck with hose attachment, soil blower truck (operated in reverse), sidewalk vacuum or hand tools (e.g., rakes and shovels) are options for each of these pretreatment devices and flow controlling/detention devices. |
Vegetated BMPs | For removing sediment from the filter beds of vegetated BMPs, use of a vacuum truck with hose attachment, soil blower truck (operated in reverse) or hand tools are options that can minimize the need to remove established vegetation, while use of a small excavator or backhoe can also be effective, but will require vegetation removal and transplanting (where feasible) or replacement after the work is completed. |
Underground BMPs | For underground BMPs (e.g., underground infiltration systems, soil cells) and associated pretreatment devices (e.g., manhole sumps, hydrodynamic/oil and grit separators, isolator rows, forebays), and in-line filters, hydro-vac trucks will likely be needed. |
For underground conveyances (i.e., catchbasins, manholes, pipes), BMPs, pretreatment devices, and in-line filters, sediment removal often requires crews performing the work to enter confined spaces. Contractors or staff performing the work must have confined space entry training to satisfy occupational health and safety requirements (Ont. Reg. 632/05 – Confined Spaces Regulation).
How the material removed from conveyances, LID BMPs, pretreatment devices and in-line filters will be safely and sustainably managed also needs consideration. Due to the small drainage area of most LID BMPs, the rate at which they accumulate sediment and associated contaminants tends to be low in comparison to centralized stormwater treatment facilities like stormwater ponds or detention chambers/tanks that receive drainage from much larger areas. As a result, the potential for sediment accumulated in LID BMPs to qualify as contaminated according to Ontario Brownfields Regulation 153/04 standards for soil and sediment (Ministry of the Environment, 2011)[4] is low.
Most often, contractors or staff performing sediment removal maintenance procedures will be cleaning multiple BMPs and pretreatment devices at multiple sites on any given day. At the end of the day, the mixture of material collected either manually, or by vacuum equipment (e.g., regenerative air or vacuum sweeper, vacuum/soil blower truck, hydro-vac truck) will include a mixture of re-usable, recyclable and non-recyclable constituents. In order to recover reusable and recyclable materials and minimize the volume of material needing to be managed otherwise, the mixture should be screened to isolate trash (for recycling or disposal), natural debris and mulch (for composting), and gravel - to pebble-sized aggregates (for washing and re-use) from finer (i.e., sand - to clay-sized) material. The sand- to clay-sized material (i.e., material passing a 2 mm diameter (ASTM No. 10) sieve) should then be assessed and managed in accordance with provincial regulations (O.Reg. 347).
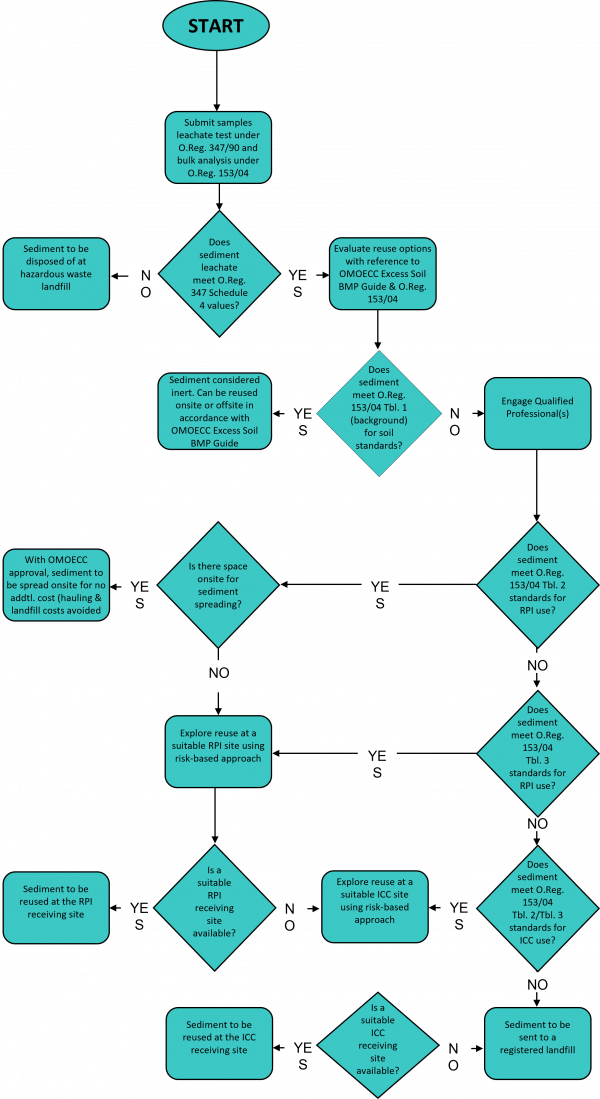
Note: This flow chart does not depict MECO policy but rather a recommended approach based on TRCA’s understanding of current MECP operational practices.
Laboratory testing to determine if beneficial reuse (e.g., spreading on landscaped areas or blending with other constituents for use as a soil conditioner) of the remaining sand- to clay-sized constituents is an option that should be considered. Determining beneficial reuse options for all constituents of the accumulated material could provide substantial savings in terms of costs associated with transporting and managing the material off-site. For more detailed guidance on what types of testing should be done on sediment accumulated in SWM BMPs and what standards to apply to determine when beneficial re-use is an option, refer to Chapter 9 of the Inspection and Maintenance Guide for Stormwater Management Ponds and Constructed Wetlands (TRCA and CH2M, 2016)[5]. The following flow chart (to the right of the page) provides an overview of the process recommended in the aforementioned guide for determining sediment reuse and disposal options.
Recommended Lab Testing for Sediment Quality[edit]
The selection of sediment quality analysis parameters should reflect the Contributing Drainage Area's (CDA) land use characteristics and reported spill history. The following are the suggested minimum lists of analytes that would be suitable for sites with no history of point source contamination. It is recommended that the MECP be contacted to determine if any spill events or other site specific circumstances would require additional analytes as well. The following step-by-step process would provide the data needed to evaluate the feasibility of beneficial use of the sediment or landfill disposal options.
1. Leachate Test[edit]
As required by O.Reg. 347, testing of leachate toxicity by the Toxicity Characteristic Leaching Procedure (TCLP), establishes whether or not the sediment is hazardous waste, which would then require proper disposal at a hazardous waste facility. The TCLP uses an acetic acid solution designed to simulate a possible worst-case leaching conditions scenario that could occur on a given study site that contains contaminated soils, or any other organic matter that will degrade over time (putrefaction) (Intrakamhaeng, et al. 2019[6]. This information is typically required by the MECP as a key first step in characterizing sediment. It may be advisable to conduct this analysis concurrently with Step 2 (O.Reg. 153/04 Bulk Soil Analysis) so that samples for both tests can be collected during the same visit.
2. O.Reg. 153/04 Bulk Soil Analysis[edit]
Bulk soil analysis based on the O.Reg. 153/04 Standard is carried out to evaluate whether sediment is suitable for beneficial use or requires landfill disposal. The OMOECC has, on a case-by-case basis, accepted the contaminant thresholds in O.Reg. 153/04 Table 1 as a basis for classifying sediment as
inert. Inert sediment can be used off-site without regulatory approval. Sediments that exceed Table 1 soil standards would require a risk evaluation to identify potential beneficial use options according to the figure to the right.
The following is a base list of bulk soil analytes to be tested. It may be necessary to include additional analytes if land use activities in the CDA or past spills are believed to have introduced contaminants that are listed in the Standards but not included in this list.
- Trace metal scan including hot water extractable boron
- Cyanide
- Polycyclic Aromatic Hydrocarbons (PAHs)
- Petroleum Hydrocarbons (PHCs)
- Sodium Adsorption Ratio (SAR)
- Electrical Conductivity (EC)
- Particle Size Distribution (PSD)
3. Topsoil Analysis and Certified Crop Advisor Report for Beneficial Use Evaluations[edit]
The topsoil analysis would only be conducted if the O.Reg. 153/04 bulk soil tests determine that the sediment does not require landfill disposal due to high contamination levels. Topsoil analysis would be necessary to demonstrate that amending the receiving site soils with the sediment would provide a benefit to the soils, as required by the Nutrient Management Act, without inhibiting plant growth.
The list of analytes to be considered includes:
- Trace metal scan including hot water extractable boron
- SAR
- EC
- pH
- Soil Organic Matter (OM)
- Extractable (i.e., Available) Nutrients
- PSD
References[edit]
- ↑ Wikimedia Commons. 2012. File:The key elements of LID.gif. http://zoe-s-wiki.wikispaces.com/Low+Impact+Development. https://commons.wikimedia.org/wiki/File:The_key_elements_of_LID.gif
- ↑ Blecken, G.T., Hunt, W.F., Al-Rubaei, A.M. Viklander, M., Lord, W.G. 2017. Stormwater control measure (SCM) maintenance considerations to ensure designed functionality. Urban Water Journal. Vol.14, No.3, 278-290. https://www.tandfonline.com/doi/full/10.1080/1573062X.2015.1111913
- ↑ DelGrosso, Z.L., Hodges, C.C., Dymond, R.L. 2019. Identifying Key Factors for Implementation and Maintenance of Green Stormwater Infrastructure. Journal of Sustainable Water in the Built Environment. 5(3): 05019002. https://ascelibrary.org/doi/10.1061/JSWBAY.0000878
- ↑ Ministry of the Environment. 2011. Soil, ground water and sediment standards for use under Part XV.1 of the Environmental Protection Act. This document provides Ontario’s soil, ground water and sediment standards effective July 1, 2011. PIBS # 7382e01. https://www.ontario.ca/page/soil-ground-water-and-sediment-standards-use-under-part-xv1-environmental-protection-act
- ↑ 5.0 5.1 Citation: Toronto and Region Conservation Authority (TRCA) and CH2M Canada. 2016. Inspection and Maintenance Guide for Stormwater Management Ponds and Constructed Wetlands. Toronto and Region Conservation Authority, Vaughan, Ontario. https://sustainabletechnologies.ca/app/uploads/2018/04/SWMFG2016_Guide_April-2018.pdf
- ↑ Intrakamhaeng, V., Clavier, K.A., Roessler, J. G., and Townsend, T. G. 2019. Limitations of the toxicity characteristic leaching procedure for providing a conservative estimate of landfilled municipal solid waste incineration ash leaching, Journal of the Air & Waste Management Association, 69:5, 623-632, DOI: 10.1080/10962247.2019.1569172